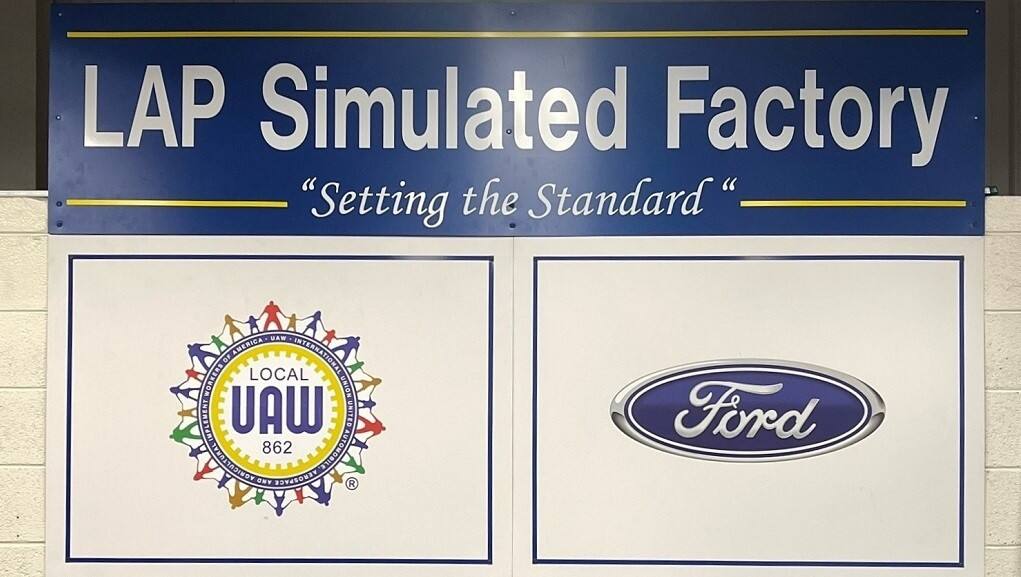
While Louisville Assembly Plant is known as the home of the Ford Escape and Lincoln Corsair, trainees in one special area of the plant watch a miniature Model T make its way down a mock assembly line. This area is known as the simulated factory – housed in the training facility behind the main building – where newly hired UAW-Ford team members learn essential skills, practicing with the small, die-cast version of the famous Ford vehicle.
Veteran plant employees know the space as “the sim lab,” which originally launched in 2011. The training lab spawned from a single-station concept developed by tool maker Jerry Cooley over a decade ago. Skilled trades and general utilities, as well as salary and hourly personnel, contributed to the project. The simulated factory’s launch was widely considered a success, and other Ford manufacturing plants have built similar training spaces at their sites to support newly hired employees as they acclimate to working on an assembly line.
When the COVID-19 pandemic hit in 2020, Louisville Assembly had to temporarily shutter the sim lab. Training development leader Erica Nevitt joined Ford Motor Company in 2021, and the desire to reopen the small-scale assembly line as an orientation resource was placed on her radar. Finally, in March 2023, the pieces fell into place and the first class was brought back to the training center.
"The training department is extremely grateful to have had so many people throughout various departments here at Louisville Assembly Plant that have supported us in this endeavor,” Nevitt says. “This truly was a team effort across the board."
Going forward, each new class will split its time between classes led by UAW training coordinator Penny Rowe, practicing in the simulated factory, and shadowing experienced assembly line workers on the plant floor.
“This is some of the new hires’ first job—they have never held a tool, much less worked in a factory. With the lab reopened, they learn how to properly hold and use the tools they will be working with every day,” Rowe explains. When the new employees finish training, she makes sure they have her phone number in case they have questions and want to reach out.
The simulated factory is already training its second class of new hires since it reopened, and employees are appreciating the hands-on training experience.