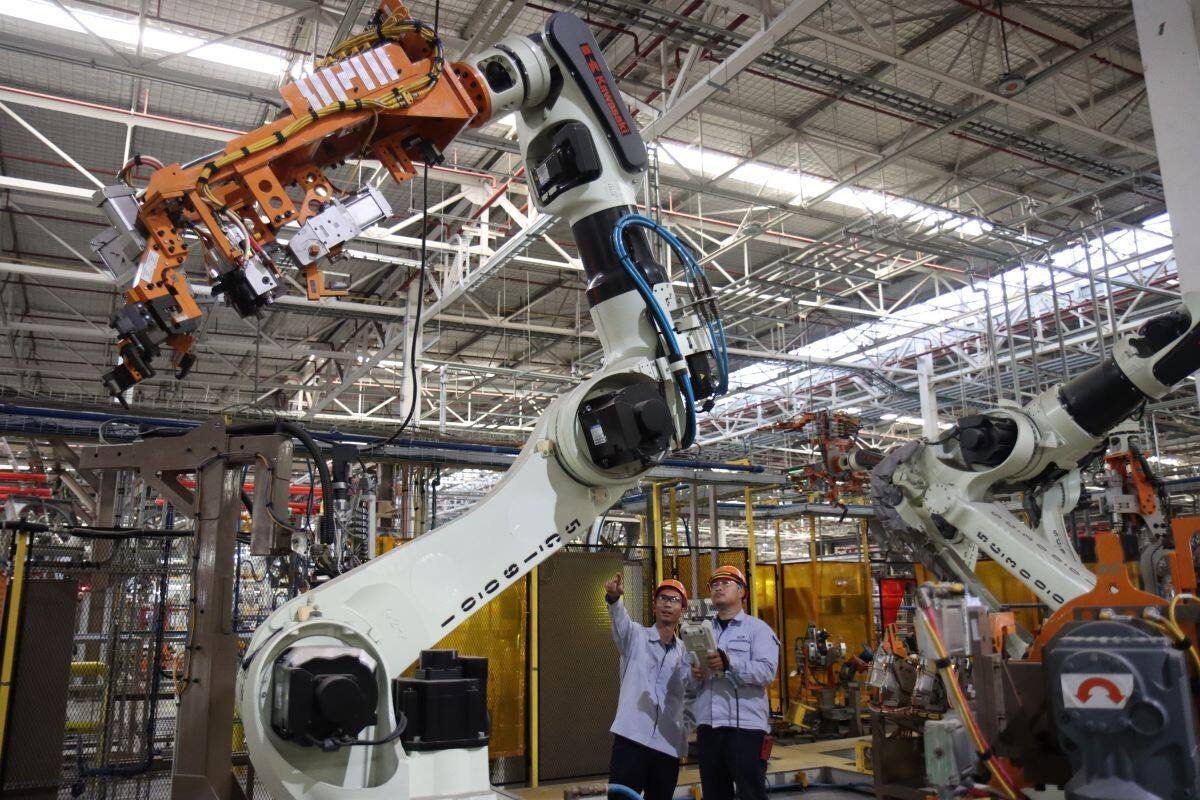
Two Ford plants in Thailand, Ford Thailand Manufacturing (FTM) and AutoAlliance Thailand (AAT), joined forces in a collaborative effort to drive continuous improvements in manufacturing facilities. Since the project kicked off last year, employees have submitted over 19,000 ideas aiming at waste reduction.
According to Supajittra Chaichotkit, the operations finance controller at Ford Thailand Manufacturing, employees at the workstation play a crucial role in identifying wasteful activities as they witness firsthand what happens each day. Certain projects have been prioritized for replication and synergy, with the potential to save the business for FTM and AAT up to $9 million.
One of the first projects was to optimize robot posture for energy savings.
The Body Shop at FTM uses advanced robots for welding, soldering, and clinching operations. However, these activities consume significant amounts of energy, leading to rising costs. Recognizing the importance of energy efficiency, the team at FTM, led by Nuttapong Chuenmee, a dedicated maintenance engineer, initiated a project named ‘Reducing Gravity Effect’. Upon its progress, Sash Stanceski, vehicle manufacturing engineer, International Markets Group, who originally researched, modelled, optimized, and created the robot repositioning paradigm, provided support and guidance for the team to focus on optimizing the posture of articulated arm robots used in the production of the popular Next-Gen Ford Ranger.
Through careful analysis of production data, Nuttapong and his team reaffirmed a fundamental engineering principle: robots consume power even when they are stationary. By adjusting the arm angle of the robots to their lowest energy idle position, they achieved a substantial reduction in energy usage – around 20 to 25 percent per robot in each cycle. Considering that FTM has a total of 208 robots, this simple adjustment has the potential to save up to 5.5 million Thai Baht ($154,000) annually. Moreover, it contributes to prolonging the lifespan of the robots' spare parts and conserving energy resources.
Nuttapong shared his insights, stating, "We don't need to create or invest in new tools or programs to reduce costs in our processes. By adhering to the principles of physics, we can simplify and bring this idea to life. It's a straightforward approach, yielding rapid results."
Sash Stanceski, the visionary behind the idea, added, "The success of this project showcases the power of applying fundamental principles. We are thrilled to witness its potential impact."
Currently, efforts are underway to replicate this project at AAT. Although the robots at AAT differ from those at FTM, the underlying concept can be adapted and implemented. The replication process is expected to be completed by the end of this year. Additionally, the Silverton plant in South Africa has expressed interest in adopting this energy-saving idea within their facilities.
The success achieved by FTM and AAT serves as a testament to the power of collaboration and employee-driven innovation. Stay tuned for more captivating stories of waste reduction as we continue our quest to enhance manufacturing efficiency and drive sustainable practices.