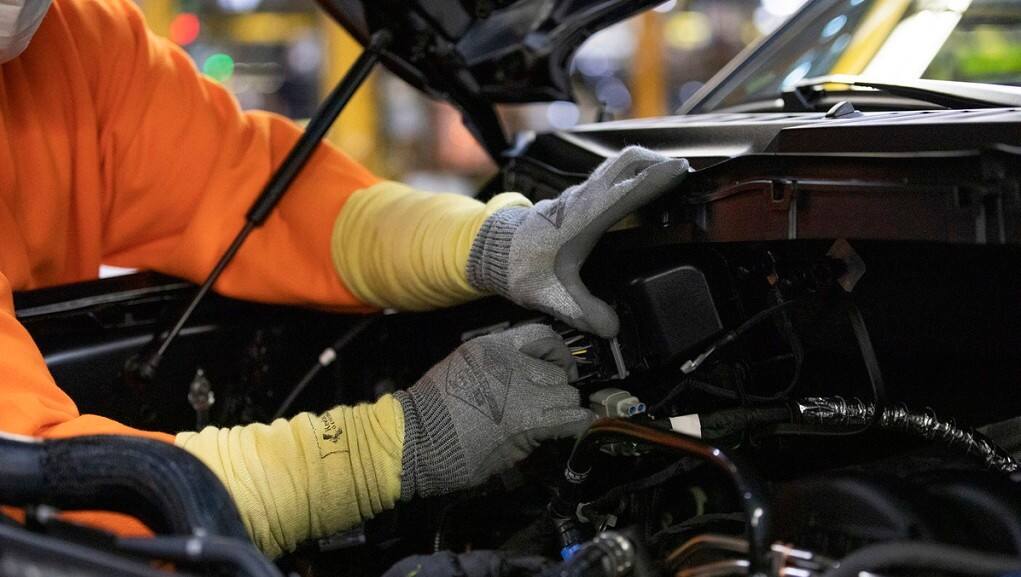
Brad Watkins knows how to pivot. Juggling late-night meetings, early-morning meetings and strategic negotiations, he’s part of a complex system at Ford that’s working hard to reduce disruptions within Ford’s intricate global supply chain.
As Ford’s director of fulfillment and delivery, Watkins is well aware of the importance of stabilizing production, both for the company and for the employees in the plants who are affected when production schedules change.
“Everyone in this company – everyone – appreciates the need for stability,” Watkins said. “We are doing everything in our power to make sure we can provide a stable production plan with reasonable lead time to give employees, suppliers and customers time to manage their lives and their business. Unfortunately, we aren’t always as successful as we’d like to be.”
Team members in the plants are frustrated with last-minute schedule changes, and senior leaders take that very seriously. Cross-functional teams are working feverishly behind-the-scenes – daily, sometimes even hourly – to strengthen the supply chain, reduce production down time and communicate updates as soon as they have line of sight. It's a monumentally complex task.
The global automotive supply chain was thrown into chaos back in 2020 when COVID-19 hit. As that situation stabilized, the semiconductor chip shortage emerged. Semiconductor chips are used extensively in today’s technology-rich vehicles, controlling everything from speed sensors to windshield-wiper motors to driver-assist systems, making them an essential part of vehicle production. The more advanced chips are used in popular electronic consumer goods like iPhones and gaming devices. With increased demand from both industries and limited capacity, competition is fierce.
Shortages aren’t limited to semiconductor-related parts. Working-level teams are in contact with suppliers almost daily, identifying delivery issues and forecasting part supplies. For key components – limited parts that are considered most significant – there is a “champion” at the senior leadership level that is responsible for working with the supplier to stabilize availability of that key component. In some cases, engineering teams are streamlining vehicle designs to make them non-dependent on a particularly scarce part.